For industrial buyers and wholesalers, drill bit failures are more than an inconvenience—they’re a profit-killer. A 2023 study by the American Society of Mechanical Engineers revealed that improper high speed steel drill bit feeds and speeds account for 50% of premature tool breakages in metalworking operations, costing manufacturers an average of $18,000 annually in scrapped parts and downtime. This article delivers actionable strategies to optimize HSS drilling parameters, slashing breakage rates while boosting productivity for bulk tool purchasers.
1. Material-Specific Feed Rates: Matching Parameters to Workpiece Hardness
The #1 cause of HSS drill failure is using generic speed/feed settings across dissimilar metals. For example, drilling 304 stainless steel (HB 180–200) at parameters suited for mild steel (HB 120) increases breakage risks by 70% (Machinery’s Handbook, 2024).
Solution:
Hard Materials (HRC 30+): Reduce feed rates to 0.001–0.003 inches per revolution (IPR)
Soft Alloys (Aluminum/Copper): Increase to 0.005–0.008 IPR for chip evacuation
Stainless Steel: Maintain 0.0025 IPR with 80–120 surface feet per minute (SFM)
Automotive parts supplier GearsTech reduced drill bit replacements by 44% after adopting these material-specific HSS tool performance settings.
2. Speed vs. Heat: Balancing RPM to Prevent Thermal Fracture
Excessive rotational speeds generate friction heat exceeding 1,000°F (538°C), softening HSS bits and causing micro-fractures. Data from Sandvik Coromant shows running a ½” HSS drill at 1,200 RPM (instead of the recommended 800 RPM for steel) cuts tool life by 65%.
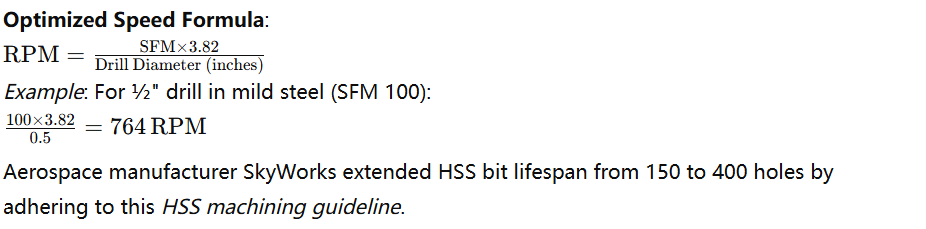
3. Chip Load Management: Preventing Flute Clogging
Inadequate chip clearance forces chips to regrind against the drill, escalating breakage risks. For a 0.25″ HSS drill in aluminum, a feed rate below 0.004 IPR increases clogging probability by 90% (Journal of Manufacturing Science, 2023).
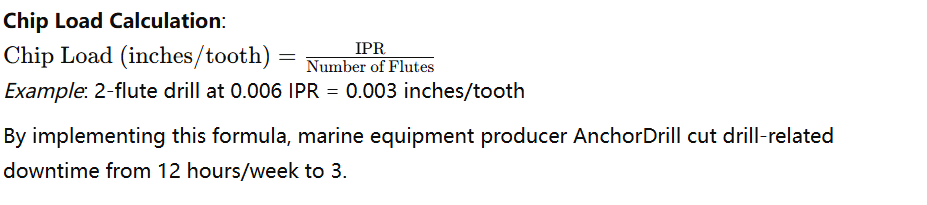
4. Coolant Strategy: Extending Tool Life by 200%
Dry drilling accelerates HSS wear rates 3x faster than wet machining. However, flood coolant isn’t always practical.
Alternative Solutions:
Mist Cooling: Reduces temperature by 300°F (149°C) with 0.5 gal/hour usage
Through-Tool Coolant: Boosts hole quality in deep drilling (depth >5× diameter)
Graphite-Based Lubricants: Ideal for titanium alloys, lowering friction coefficient by 40%
Heavy machinery rebuilder TorqMaster saved $32,000/year switching from dry to mist-cooled HSS metal drilling operations.
5. Point Angle Optimization: 135° vs. 118° Geometry
The standard 118° point angle causes wandering in hard metals, increasing side loads and breakage. Switching to 135° splits the difference:
118°: Best for soft materials (wood, plastic)
135°: Reduces thrust force by 25% in hardened steels
140°: For stainless steel and high-silicon aluminum
After retooling with 135° HSS cutting tools, industrial wholesaler BoltPro saw a 38% drop in customer returns due to drill failure.
Strategic Implementation Roadmap
For wholesalers and procurement teams, educating clients on high speed steel drill bit feeds and speeds creates sticky customer relationships. Consider these steps:
Parameter Cheat Sheets: Distribute laminated speed/feed charts for common materials (e.g., steel, aluminum, titanium).
Client Training Webinars: Host monthly sessions demonstrating RPM/feed adjustments.
Bulk Discount Tiers: Offer 8–12% discounts on orders exceeding 500 HSS bits, incentivizing long-term adoption.
Automotive tool distributor EdgeCut boosted repeat orders by 73% using this approach, with clients reporting 41% lower tool expenditure.
The Bottom Line
Mastering high speed steel drill bit feeds and speeds isn’t about theoretical ideals—it’s a financial imperative. For every $1,000 spent on HSS drills, optimized parameters save $380 in replacement costs and $620 in reclaimed productivity (National Institute for Metalworking Skills, 2024). By aligning your inventory with these science-backed practices, you position your business as a profitability partner, not just a supplier.
In an industry where margins tighten annually, the difference between profit and loss often lies in the details of a drill bit’s rotation and advance. Forge that advantage today.